Printer button two-color mold design (middle mold)
Time:2020-05-16 09:45:27 / Popularity: / Source:
1. Preface
TPE material has good slip resistance and good elastic touch, which can improve touch feel of product, enhance grip, enhance appearance of product and add value to product.
At the same time, because TPE elastomer soft rubber is a green environmentally friendly raw material, material does not contain phthalates, and does not contain halogen. Adding different toners can make beautiful products without spraying, and does not affect environment, so it is widely used.
At the same time, because TPE elastomer soft rubber is a green environmentally friendly raw material, material does not contain phthalates, and does not contain halogen. Adding different toners can make beautiful products without spraying, and does not affect environment, so it is widely used.
Figure 1 printer button product drawing
This paper introduces a brand of printer button two-color mold, in which hard rubber is HI-PS and soft rubber is TPE. These two materials have good adhesion, stable product performance, and are suitable for mass production.
2. Product analysis
Printer button product diagram is shown in Figure 1. Size is small. In product design, hard material should avoid sharp corners to ensure good contact between TPE and hard material, to improve bonding effect. Reasonably determine thickness of TPE soft rubber. If TPE is too thin, fluidity is poor, hand feel is not good. If it is too thick, it is easy to shrink, and TPE material is wasted.
3. Mold design points
Determination of number of cavities
Due to small size of product, displacement of cavity is 4 cavities. This two-color mold structure adopts Asian two-color mold structure, that is, two sets of two-color molds with same mold base. Mold base number is FCI2020, ordered from Fu Deba. Mold has two identical rear molds, and two front mold cavities are different for injecting different materials. Note that guide post guide hole of mold base still needs a reference angle offset to prevent errors during processing, just like a normal monochrome mold. Another point to note is that mold must be designed in the form of a three-plate mold. After one injection and before second injection, nozzle material needs to be separated in time. It is especially important to note that soft material of nozzle is easy to stick, and it must be paid attention to during mold design and production.
Two sets of mold bases used to make two-color mold must have same uniform size and position of guide post holes must be same. It is required that front and rear molds of two mold bases can be freely interchanged, total height of two sets of mold bases is also same, and two sets of front molds and rear molds are equally high (this requires special instructions when purchasing mold base).
Hard material HI-PS
Soft material TPE
Gate point of soft material
Gate point of hard material
Two sets of mold bases used to make two-color mold must have same uniform size and position of guide post holes must be same. It is required that front and rear molds of two mold bases can be freely interchanged, total height of two sets of mold bases is also same, and two sets of front molds and rear molds are equally high (this requires special instructions when purchasing mold base).
Hard material HI-PS
Soft material TPE
Gate point of soft material
Gate point of hard material
Gate design:
Gate location design of two-color mold is critical and needs careful consideration. This set of mold gates is a point gate. Each hole is injected at two points. Mold is a three-plate mold. Gate position is shown in product drawing. Gate position of hard material is covered by TPE when TPE is injected, and appearance is not affected. Gate location of TPE is also invisible after assembly.
Determination of shrinkage rate
Shrinkage rate of two-color mold is very critical. Generally, hard material is injected for the first time, and hard material HI-PS shrinks by 0.5%. In the monochrome mold, shrinkage rate of soft material TPE is 1-2%, and soft material shrinkage rate is obviously larger than that of hard material. It is difficult to design mold (coordinate system will not coincide when 3D parting). In two-color mold, due to limitation of hard material, soft material has a small shrinkage rate. And in small button type, soft material does not have a shrinkage rate.
Ejection of plastic parts
plastic parts are ejected by cylinder, and flow condensate is ejected by ejector pin.
See Figure 2 for water transport of front and rear molds
Water connection of two-color mold must be designed at the center of turntable. (Note that mold icon has a up side)
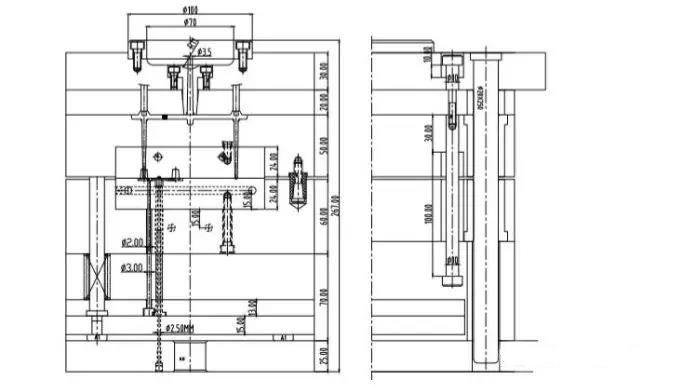
Figure 2 printer button mold drawing (hard material)
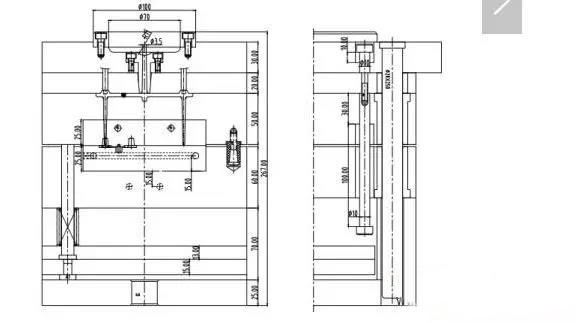
Figure 2 Printer button mold drawing (continued) (soft material)
Figure 3 Photo of printer button mold
In conclusion
Practice of customer use after export of mold shows that design of mold structure is reasonable, and provides experience for similar mold design.
Last article:Four stages of the development of home appliance molds
Next article:Do you know main points of mold trial process?
Recommended
Related
- Optimization of automotive oil pump body die-casting process04-26
- Plastic structure design 6 —part gaps, buckles and stops04-25
- Improve performance of die-casting molds and extend service life of die-casting molds04-19
- Electric vehicle front cover hot runner mold design04-19
- Automotive light bracket die-casting process analysis and mold design04-18