Causes and Countermeasures of Deformation of Injection Molded Parts- 1
Time:2024-02-19 19:46:52 / Popularity: / Source:
Introduction
1. Phenomenon of deformation
2. Nature of deformation
3. Root cause of deformation
4. Factors affecting deformation
5. Countermeasures to control deformation
6. Conclusion
7. Actual case analysis
2. Nature of deformation
3. Root cause of deformation
4. Factors affecting deformation
5. Countermeasures to control deformation
6. Conclusion
7. Actual case analysis
Introduction
For people engaged in injection mold manufacturing and injection molding, deformation of plastic parts is one of the most troublesome problems and one of main reasons for high scrap rate of products. We have been exploring true cause of deformation to find ways to control it. We use advanced computer analysis software such as moldflow and combined with industry experience to try to control deformation of plastic parts, but problem recurs again and again. Plastic material is like a wild girlfriend that is hard to figure out. Although most of time it is as gentle as water, when it gets violent it makes people helpless. Why? In final analysis, we don't know her well enough, because we don't know her well enough, we feel it's difficult to control her.
This article attempts to deeply explore real causes of plastic deformation and various factors affecting deformation from various aspects such as plastic material properties, product design, mold design, molding process, etc., so as to help us find better ways to control deformation in our work.
This article attempts to deeply explore real causes of plastic deformation and various factors affecting deformation from various aspects such as plastic material properties, product design, mold design, molding process, etc., so as to help us find better ways to control deformation in our work.
1. Plastic deformation phenomenon
Deformation phenomenon of injection molded parts refers to situation where molded products deviate from designed shape after molding. Deformation can cause:
Product function defective and unable to meet usage requirements
Product assembly problems, even if sometimes deformation can be overcome by assembly, resulting stress may cause product to crack due to external forces during use.
Product appearance problems, unable to meet appearance requirements
Other problems
Following are pictures of deformation of some common plastic molded products
Product function defective and unable to meet usage requirements
Product assembly problems, even if sometimes deformation can be overcome by assembly, resulting stress may cause product to crack due to external forces during use.
Product appearance problems, unable to meet appearance requirements
Other problems
Following are pictures of deformation of some common plastic molded products
Figure 1.1 Deformation of plastic frame requires deformation of plastic jig

Figure 1.2 Deformation of plastic thin-walled containers
Figure 1.3 Deformation of electronic products
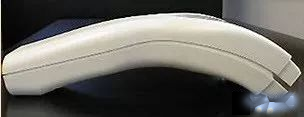
Figure 1.4 Front and bottom shell of scanner is deformed, resulting in poor assembly.
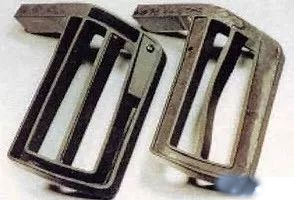
Figure 1.5 Deformation caused by poor product design: Left side shows an improved product structure with uniform wall thickness; right side shows poor product design
2. Nature of deformation
Phenomenon of plastic deformation is diverse, and its essence is role of internal stress in injection molded parts. Deviation of product from designed shape is function of force. Without action of force, product will not deviate from designed shape. Amount of deformation is determined on the one hand by size of internal stress, and on the other hand by ability of product structure to resist internal stress, that is, rigidity of product structure. Deformation of injection molded parts is essentially a release of stress, that is, internal stress of product is released to a certain extent through deformation of product.
We all know that any plastic material has a theoretical shrinkage rate, such as: ABS 0.3-0.5%, PC 0.5-0.7%, PP 1.5-2.0%, etc. This is a shrinkage rate that represents mold steel number and corresponding plastic product size. It is provided by plastic material supplier and comes from laboratory. It is only a theoretical reference data. So in actual injection molding process, will plastic material shrink 100% according to data? Is shrinkage evenly distributed within mold cavity?
Answer is obviously no. If shrinkage is 100% in accordance with design, then size of plastic part will undoubtedly faithfully reproduce design; if shrinkage is uniform, product will not deform, just like when we set shrinkage rate of product in UG or CAD, product will become larger or smaller evenly without any deformation.
Because of shrinkage characteristics of plastic materials, when molten glue fills mold cavity, material begins to cool and solidify, causing volume shrinkage. At this time, deformation begins to occur. Structure of plastic part is complex, so mold structure is also complex. It is precisely because of this complexity that during injection molding production process, there are absolute differences in melt filling speed of each area of mold cavity, pressure distribution of mold cavity, heat conduction, etc., and it is impossible to achieve an absolutely uniform state. Therefore, resulting shrinkage unevenness absolutely exists. Uneven shrinkage leads to internal stress in product and internal stress of product. Role of internal stress is essence of deformation of injection molded parts.
Uneven shrinkage definitely exists in plastic parts, so deformation of plastic parts also absolutely exists. Difference is only in degree. All our efforts are not to eliminate deformation, but to control deformation within permitted range.
We all know that any plastic material has a theoretical shrinkage rate, such as: ABS 0.3-0.5%, PC 0.5-0.7%, PP 1.5-2.0%, etc. This is a shrinkage rate that represents mold steel number and corresponding plastic product size. It is provided by plastic material supplier and comes from laboratory. It is only a theoretical reference data. So in actual injection molding process, will plastic material shrink 100% according to data? Is shrinkage evenly distributed within mold cavity?
Answer is obviously no. If shrinkage is 100% in accordance with design, then size of plastic part will undoubtedly faithfully reproduce design; if shrinkage is uniform, product will not deform, just like when we set shrinkage rate of product in UG or CAD, product will become larger or smaller evenly without any deformation.
Because of shrinkage characteristics of plastic materials, when molten glue fills mold cavity, material begins to cool and solidify, causing volume shrinkage. At this time, deformation begins to occur. Structure of plastic part is complex, so mold structure is also complex. It is precisely because of this complexity that during injection molding production process, there are absolute differences in melt filling speed of each area of mold cavity, pressure distribution of mold cavity, heat conduction, etc., and it is impossible to achieve an absolutely uniform state. Therefore, resulting shrinkage unevenness absolutely exists. Uneven shrinkage leads to internal stress in product and internal stress of product. Role of internal stress is essence of deformation of injection molded parts.
Uneven shrinkage definitely exists in plastic parts, so deformation of plastic parts also absolutely exists. Difference is only in degree. All our efforts are not to eliminate deformation, but to control deformation within permitted range.
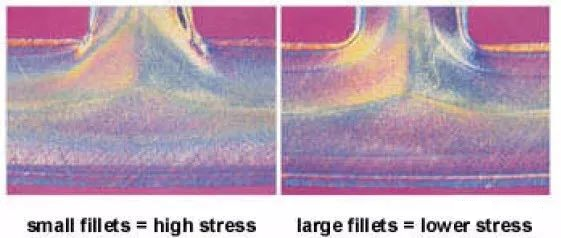
Figure 2.1 Residual stress distribution at the root of ribs of a transparent product under polarized light irradiation. Picture on the left has a smaller rounded corner, so residual stress is larger; picture on the right shows a larger rounded corner, and residual stress is smaller.
Figure 2.2 shows stress distribution of transparent CD box products
3. Root cause of deformation
To discuss this issue clearly, we must first start with plastic materials, starting with polymer structure of plastic materials. Without understanding this, we have no way of truly understanding cause of deformation.
We all know that plastic is a polymer material with long molecular chains and large molecular weight. It has a very long main chain and branch chains on the edges of main chain, as shown in following figure:
We all know that plastic is a polymer material with long molecular chains and large molecular weight. It has a very long main chain and branch chains on the edges of main chain, as shown in following figure:
Figure 3.1 A 3D model of a molecular monomer of amorphous plastic PC
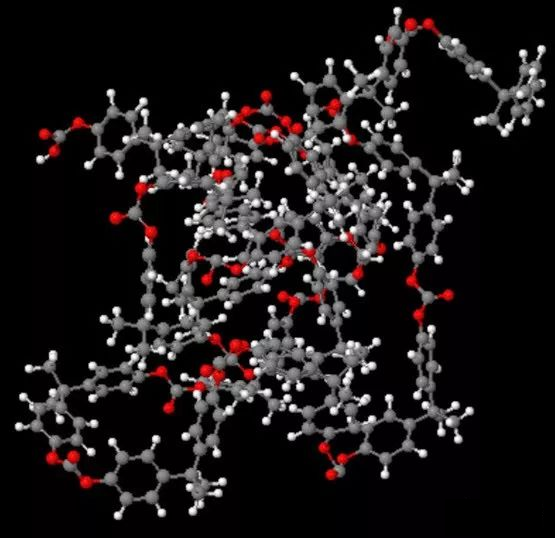
Figure 3.2 A 3D model of molecular chain structure of a non-crystalline plastic PC
Figure 3.3 A 3D model of molecular chain of semi-crystalline plastic PA66
These are molecular microstructures that can only be observed with help of a high-end microscope. Text descriptions are feeble. You have to see real thing to have an intuitive impression. But observing and studying molecular structure in a microscopic state is what laboratory needs to do. For us plastic users, we do not have conditions to observe these with help of a microscope every day.
Molecular chain structure of plastic determines type of plastic material. General characteristics of plastic are: the larger molecular weight, the longer molecular chain, the poorer fluidity of plastic, and the more difficult it is to mold, so its mechanical properties such as strength and impact resistance are better. This description is very abstract. In order to better understand this sentence, we need to use our unlimited imagination: imagine a plastic molecule as an earthworm. This creates many images and helps us explain some forming principles or phenomena.
For example: a piece of PC raw material is made up of countless long and large earthworms that are tightly entwined together, have been frozen at low temperatures and lose their activity, while a PC material product is more earthworms tightly wound together (non-crystalline plastic) or arranged in an orderly manner (semi-crystalline plastic); an ABS raw material is countless earthworms of same length and size, tightly entangled together, frozen and lost their activity. When material pellets are heated, these frozen earthworms gradually regain their activity and slowly stretch out until they can flow. Then they can enter mold cavity driven by screw of injection molding machine and freeze again to become product we need. Length of molecular chain is length of earthworm, and mass of molecular chain is mass of earthworm. It is difficult for large earthworms to flow, but it is easy for small earthworms to flow. When large earthworms are entangled together, the greater force, the better mechanical strength of plastic. The tighter earthworms are entangled, the more resistant they are to external forces, which means strength of product.
These are molecular microstructures that can only be observed with help of a high-end microscope. Text descriptions are feeble. You have to see real thing to have an intuitive impression. But observing and studying molecular structure in a microscopic state is what laboratory needs to do. For us plastic users, we do not have conditions to observe these with help of a microscope every day.
Molecular chain structure of plastic determines type of plastic material. General characteristics of plastic are: the larger molecular weight, the longer molecular chain, the poorer fluidity of plastic, and the more difficult it is to mold, so its mechanical properties such as strength and impact resistance are better. This description is very abstract. In order to better understand this sentence, we need to use our unlimited imagination: imagine a plastic molecule as an earthworm. This creates many images and helps us explain some forming principles or phenomena.
For example: a piece of PC raw material is made up of countless long and large earthworms that are tightly entwined together, have been frozen at low temperatures and lose their activity, while a PC material product is more earthworms tightly wound together (non-crystalline plastic) or arranged in an orderly manner (semi-crystalline plastic); an ABS raw material is countless earthworms of same length and size, tightly entangled together, frozen and lost their activity. When material pellets are heated, these frozen earthworms gradually regain their activity and slowly stretch out until they can flow. Then they can enter mold cavity driven by screw of injection molding machine and freeze again to become product we need. Length of molecular chain is length of earthworm, and mass of molecular chain is mass of earthworm. It is difficult for large earthworms to flow, but it is easy for small earthworms to flow. When large earthworms are entangled together, the greater force, the better mechanical strength of plastic. The tighter earthworms are entangled, the more resistant they are to external forces, which means strength of product.
Figure 3.4 Molecular structures of three physical states of amorphous plastics and (semi-)crystalline plastics. Molecules of amorphous plastics are tightly and disorderly entangled below TG; molecules of (semi-)crystalline materials below TG are partly ordered and partly randomly entangled. There is no difference in molecular chain in molten state.
Crystalline plastic is actually semi-crystalline plastic. In practice, it is difficult for all molecules to crystallize, so it is called semi-crystalline plastic.
We only need to figure out what happens to these earthworms when they are injected into mold cavity and cooled after being injected into mold cavity, and we will understand true cause of deformation. We first need to understand that these earthworms have such characteristics:
(To be continued: Series 2. A paragraph will be released every week. If you are interested, you can add GudMould and continue to pay attention.)
Crystalline plastic is actually semi-crystalline plastic. In practice, it is difficult for all molecules to crystallize, so it is called semi-crystalline plastic.
We only need to figure out what happens to these earthworms when they are injected into mold cavity and cooled after being injected into mold cavity, and we will understand true cause of deformation. We first need to understand that these earthworms have such characteristics:
(To be continued: Series 2. A paragraph will be released every week. If you are interested, you can add GudMould and continue to pay attention.)
Recommended
Related
- Design of pouring and overflow system of die casting mold07-27
- Design of coated wire for wire EDM07-27
- Multiple cases describe design and manufacture of die castings without flash burrs07-26
- Principles for selecting injection molding machines07-26
- Research and application of technology to reduce cracks in die-casting molds07-25