Know a plastic raw material every day - LCP plastic
Time:2024-01-25 18:59:32 / Popularity: / Source:
Full name of LCP plastic raw material is LIQUID CRYSTAL POLYMER. It is a new type of polymer material that generally exhibits liquid crystallinity in molten state. These materials have excellent heat resistance and molding processability. Polymerization method is mainly based on melt polycondensation, and solid phase polycondensation is often supplemented by fully aromatic LCP to obtain high molecular weight products.
LCP is a new class of polymers with outstanding properties. LCPs are a broad class of materials that include:
a, lyotropic liquid crystal: need to be processed in solution;
b. Thermotropic liquid crystal: can be processed in molten state.
LCP appearance: beige (also has white opaque solid powder);
LCP density: 1.35-1.45g/cm³;.
Heat resistance classification of liquid crystal resins (low, medium and high heat resistance types)
Low heat resistance <177, medium heat resistance 177-243, high heat resistance >243.
a, lyotropic liquid crystal: need to be processed in solution;
b. Thermotropic liquid crystal: can be processed in molten state.
LCP appearance: beige (also has white opaque solid powder);
LCP density: 1.35-1.45g/cm³;.
Heat resistance classification of liquid crystal resins (low, medium and high heat resistance types)
Low heat resistance <177, medium heat resistance 177-243, high heat resistance >243.
Characteristic
a. LCP has self-reinforcing properties: it has characteristics of an unusual and uniform fibrous structure, so unreinforced liquid crystal plastics can reach or even exceed mechanical strength and modulus of ordinary engineering plastics reinforced with tens of percent of glass fibers . If it is reinforced with glass fiber, carbon fiber, etc., it is far more than other engineering plastics.
b. Liquid crystal polymers also have excellent thermal stability, heat resistance and chemical resistance. Creep characteristics of most plastics are negligible for liquid crystal materials, and they are excellent in wear resistance and wear reduction.
c. LCP has good weather resistance and radiation resistance, has excellent flame retardancy, and can extinguish flame without continuing to burn. Its combustion grade reaches UL94V-0 level.
d. LCP has excellent electrical insulation properties. Its dielectric strength is higher than that of general engineering plastics, and its arc resistance is good. In continuous use temperature of 200-300 ℃, its electrical properties are not affected. Intermittent use temperature can reach about 316℃.
e. LCP has outstanding corrosion resistance. LCP products will not be eroded in presence of 90% acid and 50% alkali. For industrial solvents, fuel oils, detergents and hot water, they will not be dissolved after contact and will not cause stress cracking.
b. Liquid crystal polymers also have excellent thermal stability, heat resistance and chemical resistance. Creep characteristics of most plastics are negligible for liquid crystal materials, and they are excellent in wear resistance and wear reduction.
c. LCP has good weather resistance and radiation resistance, has excellent flame retardancy, and can extinguish flame without continuing to burn. Its combustion grade reaches UL94V-0 level.
d. LCP has excellent electrical insulation properties. Its dielectric strength is higher than that of general engineering plastics, and its arc resistance is good. In continuous use temperature of 200-300 ℃, its electrical properties are not affected. Intermittent use temperature can reach about 316℃.
e. LCP has outstanding corrosion resistance. LCP products will not be eroded in presence of 90% acid and 50% alkali. For industrial solvents, fuel oils, detergents and hot water, they will not be dissolved after contact and will not cause stress cracking.
Application
a. Electronic and electrical is main market of LCP: electronic and electrical surface assembly welding technology has high requirements on dimensional stability and heat resistance of material (can withstand vapor phase welding and infrared welding used in surface assembly technology);
b, LCP: flexible printed circuit boards, satellite electronic components, jet engine parts, automotive mechanical parts, medical aspects;
c. LCP is added with high filler or alloy (PSF/PBT/PA):
As an integrated circuit packaging material, it can replace epoxy resin as a packaging material for coil skeletons; as a fiber optic cable connector sheath and high-strength components, instead of ceramics as a filling material in chemical separation towers; instead of glass fiber reinforced polysulfone and other plastics ( Panels on exterior of spacecraft, braking systems on exterior of automobiles).
LCP has been used in microwave containers, can withstand high and low temperatures. LCP can also be used for printed circuit boards, satellite electronic components, jet engine parts: for electrical, electronic and automotive mechanical parts or components; it can also be used in medical applications.
LCP can be added with high filler as integrated circuit packaging material to replace epoxy resin as packaging material of coil skeleton; used as fiber optic cable connector head cover and high-strength components; instead of ceramics as filling material in chemical separation towers, etc. LCP can also be blended with polysulfone, PBT, polyamide and other plastics to make alloys, and parts have high mechanical strength after molding.
b, LCP: flexible printed circuit boards, satellite electronic components, jet engine parts, automotive mechanical parts, medical aspects;
c. LCP is added with high filler or alloy (PSF/PBT/PA):
As an integrated circuit packaging material, it can replace epoxy resin as a packaging material for coil skeletons; as a fiber optic cable connector sheath and high-strength components, instead of ceramics as a filling material in chemical separation towers; instead of glass fiber reinforced polysulfone and other plastics ( Panels on exterior of spacecraft, braking systems on exterior of automobiles).
LCP has been used in microwave containers, can withstand high and low temperatures. LCP can also be used for printed circuit boards, satellite electronic components, jet engine parts: for electrical, electronic and automotive mechanical parts or components; it can also be used in medical applications.
LCP can be added with high filler as integrated circuit packaging material to replace epoxy resin as packaging material of coil skeleton; used as fiber optic cable connector head cover and high-strength components; instead of ceramics as filling material in chemical separation towers, etc. LCP can also be blended with polysulfone, PBT, polyamide and other plastics to make alloys, and parts have high mechanical strength after molding.
Injection molding process
Due to great difference in performance and use level after modification, its processing technology is also very variable.
1. LCP material should be dried before use, temperature is about 140 ℃, time is about 4~24 hours, residual moisture content of LCP material after dehumidification should be below 0.02%, and dew point should be kept at -35 ℃.
2. Barrel temperature
Usually barrel temperature, nozzle temperature, and material melting temperature are shown in figure below.
Resin drying conditions | temperature | About 140 |
time | 4-24 hours | |
Tube temperature (℃) | Back | 330-350 |
Middle | 350-370 | |
Front | 370-390 | |
Nozzle | 370-390 | |
Suitable resin temperature (℃) | 380 | |
Mold temperature (℃) | 40-160 | |
Injection pressure (MPa) | 120-160 | |
Holding pressure (MPa) | 40-60 | |
Screw back pressure (MPa) | 0-5 | |
Injection speed | medium to high speed | |
Screw speed (RPM) | 100-150 |
Considering service life of screw, temperature difference between rear, middle and front can be reduced. To prevent nozzle drooling, nozzle temperature can be 10℃ lower than temperature shown in table, or 20℃ higher than temperature shown in table if flowability is to be improved.
3. Mold temperature
(1) Mold design of LCP products is very important. Plastic inlet of mold should be an ordinary open mouth instead of a hot nozzle. If hot nozzle product is used, it is easy to foam, that is, if temperature is too high, product may be overheated.
(2) Generally, temperature of mold is about 40~140℃, and temperature of front mold should be higher than that of back mold. Because temperature of front mold is high, fluidity of molten glue is good, and it is not easy to cause cold glue. Temperature of back mold is low, product is easy to crystallize and form, temperature difference between front and rear molds does not exceed 15 ℃.
(3) In terms of mold temperature selection, a lower mold temperature should be selected in order to shorten molding cycle and prevent flashing; if dimensional stability of product is required to be high to reduce occurrence of seams and insufficient filling, a higher mold temperature should be selected.
(2) Generally, temperature of mold is about 40~140℃, and temperature of front mold should be higher than that of back mold. Because temperature of front mold is high, fluidity of molten glue is good, and it is not easy to cause cold glue. Temperature of back mold is low, product is easy to crystallize and form, temperature difference between front and rear molds does not exceed 15 ℃.
(3) In terms of mold temperature selection, a lower mold temperature should be selected in order to shorten molding cycle and prevent flashing; if dimensional stability of product is required to be high to reduce occurrence of seams and insufficient filling, a higher mold temperature should be selected.
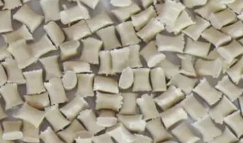
4. Plasticization
LCP barrel screw needs to be specially designed with alloys and has high wear resistance and corrosion resistance. Compression ratio, length-diameter ratio and thread of screw have special requirements. Gap between material tube and screw is the key, which is different from design of general plastic material tube and screw, otherwise feeding will be more difficult. Nozzle generally adopts an open design, which requires precise temperature control and avoids use of closed nozzles.
Rotational speed of screw is generally 100 rpm. If it is a material containing glass fiber or carbon glass fiber, in order to prevent glass fiber from being broken, we must choose a relatively low speed. Also, keep back pressure as low as possible.
When barrel temperature is set to 300 ℃, residence time of material in barrel will affect mechanical properties and color. Unpacked grade was held in barrel for 15 minutes with a slight decrease in mechanical properties.
a. LCP material has good fluidity but relatively fast crystallization. In addition, LCP itself moves in a straight line. Flow ratio of straight line and horizontal line is 1:10, and general material is 1:2~3, which requires injection molding machine to have a higher injection speed.
b. In order to meet requirements of high speed and sensitivity, injection unit of Jijian LCP injection molding machine is specially designed, which is also one of the most critical parts.
c. Injection pressure and injection speed. The most appropriate injection pressure depends on material, product shape, mold design gate and runner, etc. However, viscosity of LCP after melting is very low, so injection pressure is lower than that of ordinary resins. Curing time of LCP is relatively fast, so high-speed injection is an important requirement for injection molding machine, especially for Bobbin products. The smaller and thinner product, the more troublesome it is, and injection speed should be much higher than injection pressure.
d. Speed of screw is generally 100~150rpm. If it is a material containing glass fiber or carbon glass fiber, in order to prevent glass fiber from being broken, speed should be reduced accordingly.
Rotational speed of screw is generally 100 rpm. If it is a material containing glass fiber or carbon glass fiber, in order to prevent glass fiber from being broken, we must choose a relatively low speed. Also, keep back pressure as low as possible.
When barrel temperature is set to 300 ℃, residence time of material in barrel will affect mechanical properties and color. Unpacked grade was held in barrel for 15 minutes with a slight decrease in mechanical properties.
a. LCP material has good fluidity but relatively fast crystallization. In addition, LCP itself moves in a straight line. Flow ratio of straight line and horizontal line is 1:10, and general material is 1:2~3, which requires injection molding machine to have a higher injection speed.
b. In order to meet requirements of high speed and sensitivity, injection unit of Jijian LCP injection molding machine is specially designed, which is also one of the most critical parts.
c. Injection pressure and injection speed. The most appropriate injection pressure depends on material, product shape, mold design gate and runner, etc. However, viscosity of LCP after melting is very low, so injection pressure is lower than that of ordinary resins. Curing time of LCP is relatively fast, so high-speed injection is an important requirement for injection molding machine, especially for Bobbin products. The smaller and thinner product, the more troublesome it is, and injection speed should be much higher than injection pressure.
d. Speed of screw is generally 100~150rpm. If it is a material containing glass fiber or carbon glass fiber, in order to prevent glass fiber from being broken, speed should be reduced accordingly.
5. Injection molding control process of LCP material
a. Adopt proportional back pressure to make feeding more accurate and stable.
B. Back pressure can be used for large products, and 0 for small products.
c. If back pressure of large products is small, density will be relatively small, and surface gloss will be poor.
d. High-sensitivity injection system and automatic V-P (V injection pressure, P holding pressure) conversion function make product precise and stable. If necessary (such as product is very precise), it is recommended to install a pressure sensor at gate of mold cavity. Makes V-P switching closer to reality.
e. Pressure holding time of beer plane product should not be too long, otherwise it will easily cause product to warp, deform and generate stress.
f. If LCP material stays in material tube for a long time or residual amount is too large, it is easy to carbonize LCP material, and there will be bubbles on the surface of product. Generally, mold is opened within 3 seconds after melting of material pipe, and residual amount is guaranteed to be within 5mm.
g. If machine is stopped and re-molded, waste material in material pipe needs to be ejected.
h. Molding cycle depends on size, shape, thickness, mold structure and molding conditions of product. LCP material has good fluidity, so filling time is relatively short, and crystallization molding speed is relatively fast, so molding cycle is relatively short.
B. Back pressure can be used for large products, and 0 for small products.
c. If back pressure of large products is small, density will be relatively small, and surface gloss will be poor.
d. High-sensitivity injection system and automatic V-P (V injection pressure, P holding pressure) conversion function make product precise and stable. If necessary (such as product is very precise), it is recommended to install a pressure sensor at gate of mold cavity. Makes V-P switching closer to reality.
e. Pressure holding time of beer plane product should not be too long, otherwise it will easily cause product to warp, deform and generate stress.
f. If LCP material stays in material tube for a long time or residual amount is too large, it is easy to carbonize LCP material, and there will be bubbles on the surface of product. Generally, mold is opened within 3 seconds after melting of material pipe, and residual amount is guaranteed to be within 5mm.
g. If machine is stopped and re-molded, waste material in material pipe needs to be ejected.
h. Molding cycle depends on size, shape, thickness, mold structure and molding conditions of product. LCP material has good fluidity, so filling time is relatively short, and crystallization molding speed is relatively fast, so molding cycle is relatively short.
Recommended
Related
- Design of pouring and overflow system of die casting mold07-27
- Design of coated wire for wire EDM07-27
- Multiple cases describe design and manufacture of die castings without flash burrs07-26
- Principles for selecting injection molding machines07-26
- Research and application of technology to reduce cracks in die-casting molds07-25